At the heart of the Chrysler Technology Center, Stellantis has created a virtual reality laboratory that is revolutionizing production processes. Near the pilot plant where the first examples of new models come to life, this high-tech space blends digital simulation and industrial precision to make vehicle assembly faster, more efficient, and safer.
Stellantis is redesigning the future of production thanks to virtual reality
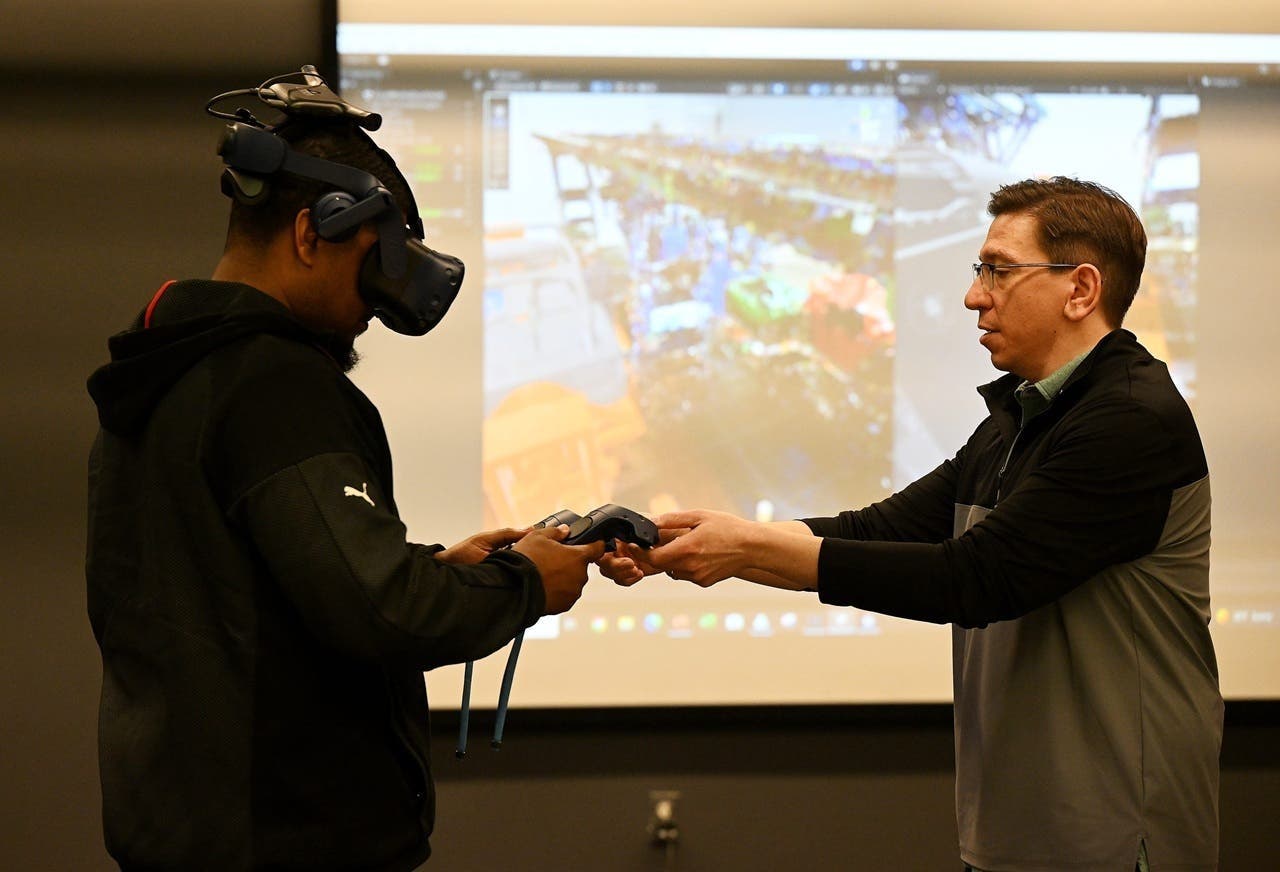
Inaugurated in 2018, the laboratory has been continuously improved, becoming one of the most advanced centers for immersive innovation in the automotive sector. Integrating tools such as motion capture, physical simulation of components, and digital twins, Stellantis has drawn inspiration from sectors like architecture, cinema, and video game development to optimize production quality and refine plant organization.
“Production is at the core of our business,” said Tim Fallon, Senior Vice President for Production in North America. “Advanced technologies like virtual reality allow us to anticipate problems, improving the safety of our facilities and ensuring excellent quality for our customers.”
The laboratory also plays a crucial role in ergonomic analysis: by virtually simulating the work environment, teams can study operator movements, refine equipment layout, and define so-called “golden zones” for greater accessibility and less physical strain.
The space, which extends over 12×13 meters, with an operational area of 6×7 meters, has become the focal point of Stellantis‘ digital engineering efforts. Thanks to virtual reality, the company has resolved hundreds of critical issues even before vehicles entered production. A significant example comes from the Sterling Heights and Warren Truck plants, where VR simulation has made it possible to precisely establish the ideal height of vehicles to facilitate the assembly of electrical connections under the chassis, thus improving ergonomics and safety.
Alongside immersive simulations, Stellantis also leverages 3D printing to accelerate component prototyping, reduce waste materials, and increase efficiency. The goal now is to extend these technologies globally, pushing the entire group toward smarter and more sustainable production.